It’s not even 9 a.m. and the construction site is bustling. A concrete foundation is being poured in the bottom of a large pit where a multistory residential building will soon rise. Somewhere out of sight a jackhammer adds to the rumbling symphony of trucks. A nearby building is also being renovated and there are many teams working diligently across the site.
BMP Inspectors
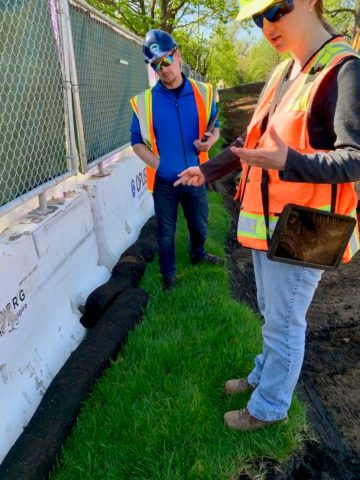
Hardhat and safety glasses on, I follow Elizabeth and Ari past a resting excavator and into the office trailer to check in with the site supervisor. Elizabeth and Ari are Best Management Practices (BMP)¹ Inspectors, part of Capitol Region Watershed District’s (CRWD) Regulatory Division. At any given time, they are each responsible for permits at several active sites like the one we are visiting this morning. CRWD issues permits² to construction site owners and their operators to ensure stormwater runoff from development projects does not negatively impact water quality in the District’s lakes, wetlands and the Mississippi River.
Stormwater Pollutant Prevention Plan
Inside the office trailer the site supervisor says a brief hello and continues with a meeting, already familiar with visits from CRWD Inspectors. Ari reviews the Stormwater Pollutant Prevention Plan (SWPPP) log, a requirement of the Minnesota Pollution Control Agency (MPCA). It requires construction site supervisors to check their sites regularly for key BMPs for erosion and sediment control. This is done at least once every seven days, and after a rainfall of .5” or more. The site supervisors take notes, and flag areas for maintenance or corrective action.
Water runoff to storm drains travels untreated to area lakes, wetlands and the Mississippi River. Ensuring water runoff entering storm drains is as clean as possible is vital to the water quality both in the District and along Mississippi River all the way to the Gulf of Mexico.
Perimeter and Inlet Controls
Going outside, we begin to walk the perimeter of the site. Elizabeth notes that vegetation ditches are being effectively used to control water runoff, and that the black mesh silt logs are properly overlapped to stop any overflow. Various perimeter controls can be used at construction sites and should contain all downhill boundaries of the site to stop or slow water from washing away, giving the water time to soak into the ground. Ari uses a tablet to make notes and take pictures to send later with the report.
Along an adjacent busy street we see evidence of soil erosion on the boulevard that would impact the surrounding storm drains. Brightly colored inlet controls are installed in any storm drains that may be impacted by runoff from the project site. Ari and Elizabeth check to ensure the liners have been correctly installed and are being adequately cleaned. Elizabeth points out an additional drain down the street from the construction site – it’s at a low point and would drain water runoff from the area. The inspection report will note this and ask the site supervisor to add an inlet control. Preventing sediment and debris from entering storm drains is important for water quality in our lakes and the Mississippi River.
Washout
A leak-proof basin used for concrete washout has overflowed at one spot. Ari takes a picture and makes a note. Concrete washouts are a major area of concern for water quality from construction sites. Concrete mixer trucks need to be cleaned out soon after they have emptied, and this washout water needs be contained in a liner or tank, so it doesn’t contaminate our groundwater, lakes and the Mississippi River. Elizabeth explains that evidence of improper wash-out are always something the BMP Inspectors look for. The washout remnants can be easily seen on dirt and grass. The liquid concrete waste is very mobile to surface waters, like lakes, wetlands and rivers, as well as into the groundwater, making it a major pollution concern.
Soil Stabilization
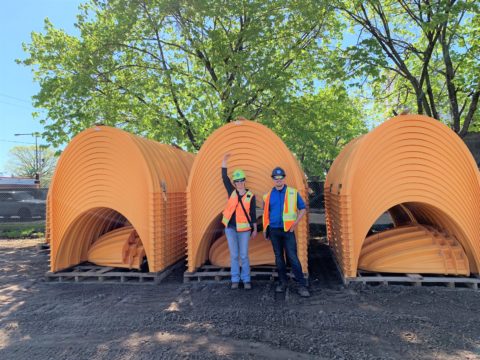
Topsoil is piled in one corner of the site. It will be used elsewhere in the project but not until a later phase. To prevent erosion of the pile a seeding spray has been applied and grass is already beginning to sprout. The spray helps holds the soil in place while the grass roots are getting established, without the vegetation like grass or another covering the soil would quickly wash away in a rainstorm. Elizabeth and Ari see some areas where the seedlings have not been able to contain erosion. More seed will need to be applied.
Entrances
Vehicles leaving the site can carry dirt and debris into the road which will then wash to storm drains. To control this issue exits are covered by rocks, mulch or measures like pads, acting almost like a doormat to trap the dirt from the tires. Even with rocks or mulch there may still be dirt tracked into the street. Any track-out that does occur should be removed within 24 hours, or earlier if rain is forecasted. The BMP Inspectors review the exits and recommend any changes. As we walk, Ari and Elizabeth look for anything that could leak, like propane tanks. Even waste receptacles are noted if there is trash around. Anything on the ground can end up in our water.
Permanent Stormwater System
Large yellow-orange half pipes sit stacked along a fence. This is the stormwater capture system that will be installed in the coming weeks. Elizabeth looks at the installation plans with the site supervisor. She gives some suggestions for installation, and reminders on some of the materials that are best, and things to avoid. When possible, CRWD Inspectors are present for installation to assist with any questions and to ensure plans are followed. The system will capture water run-off from the roof and parking lots once the building and surrounding areas are complete. The first 1.1 inches of rain over all impervious surfaces is required to be captured and infiltrated on site, capturing most of the dirtiest water. Some permittees choose to go beyond the requirements and include innovative projects³ like the rainwater reuse systems at Allianz Field and CHS Field.
Reporting
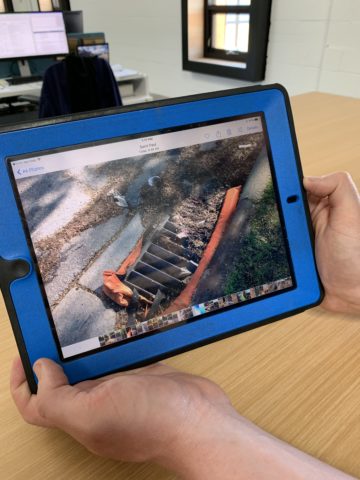
Back at the office Ari prepares an Erosion & Sediment Control Inspection Report for each site he has visited that day. Using the notes and photos, he reviews the site in each of the following areas:
• Perimeter controls
• Entrance
• Sediment tracking
• Soil stabilization
• Concrete washout
• Inspections & SWPPP updates
• Dewatering (pumping standing water) should be clear, by the naked eye (using an informal bottle test‡)
• Other notes
The report generates into a PDF that is sent to all relevant contacts, including the construction site supervisors. Communications are saved in a file for each open permit. In CRWD there are about 50-60 active permit sites at peak summer season (see the Active Permits map). Permits remain open until they are closed out, which may take years depending on the site. Some sites reaching the close-out phase in the summer of 2019 began construction in 2012-2013.
Elizabeth and Ari send their reports from their morning site visits. Each head back out to another round of inspections. Stormwater management is critical to improving water quality. With continuous construction throughout a highly urbanized area CRWD’s Regulatory Division is crucial to protecting the water quality in the District.
To view a map of active permits in CRWD visit our Permits page. Check out MPCA’s 10 Steps to Stormwater Pollution Prevention on Small Residential Construction Sites for an illustration of some of the BMPs mentioned above.
1 BMPs stands for Best Management Practices. BMPs are the preferred tools to manage water runoff and can address all three primary stormwater concerns; rate, volume and quality. BMPs refer to temporary erosion and sediment control and permanent stormwater capture.
2 Impervious or paved surfaces on new development projects generate large volumes of runoff that may contain oil, salt, dirt, bacteria and trash, all of which contribute to poor water quality in CRWD. The Permitting Program regulates construction sites that are more than one acre. CRWD requires erosion and sediment control during construction and installation of Best Management Practices (BMPs) to treat runoff after construction. For details, please visit the Permits section on our website.
3 CRWD’s Water Quality Capital Improvement Grants provide financial assistance for final engineering and construction of cost-effective and/or innovative projects that protect and improve the water quality of waterbodies within CRWD.
‡ Water clarity is measured in Nephelometric Turbidity Units (NTU). Drinking water in the United States, for example, is 1.0 NTU or lower. Turbid water may have 600 NTU or higher. The clear bottle test is a very informal way to measure the clarity of the water. Ari explains that a clear bottle is filled (like an empty water or soda bottle) and you should still be able to see your hand through the bottle. He shows an example of a water runoff sample he took from one of his permit sites during a rainstorm a week before. The bottle has been sitting undisturbed on his desk for several days and the water is still extremely cloudy, and we can barely see a hand through the other side. This concentrated mix of construction dust and soil is exactly what we want to avoid going into the storm sewer system and reaching our lakes and the Mississippi River. The faster the sediment in the bottle settles, the more likely the site would be able to clean the water to an acceptable standard to pump off site.